[Last updated 10/9/24 9:14 PM PT—Photos of Norton Simon Museum in Pasadena added at bottom of post]
Back in January of this year, I was planning a return trip to San Francisco—a city I hadn't spent the weekend in since 2006 (although I spent a few hours there a couple of years ago).
I had a lot of catching up to do.
Since I don't visit the Bay Area very often, I don't have a huge list of places to visit—so I fell back on my tried-and-true methods of seeking out fun activities.
And that meant looking for one of my go-to's, factory tours.
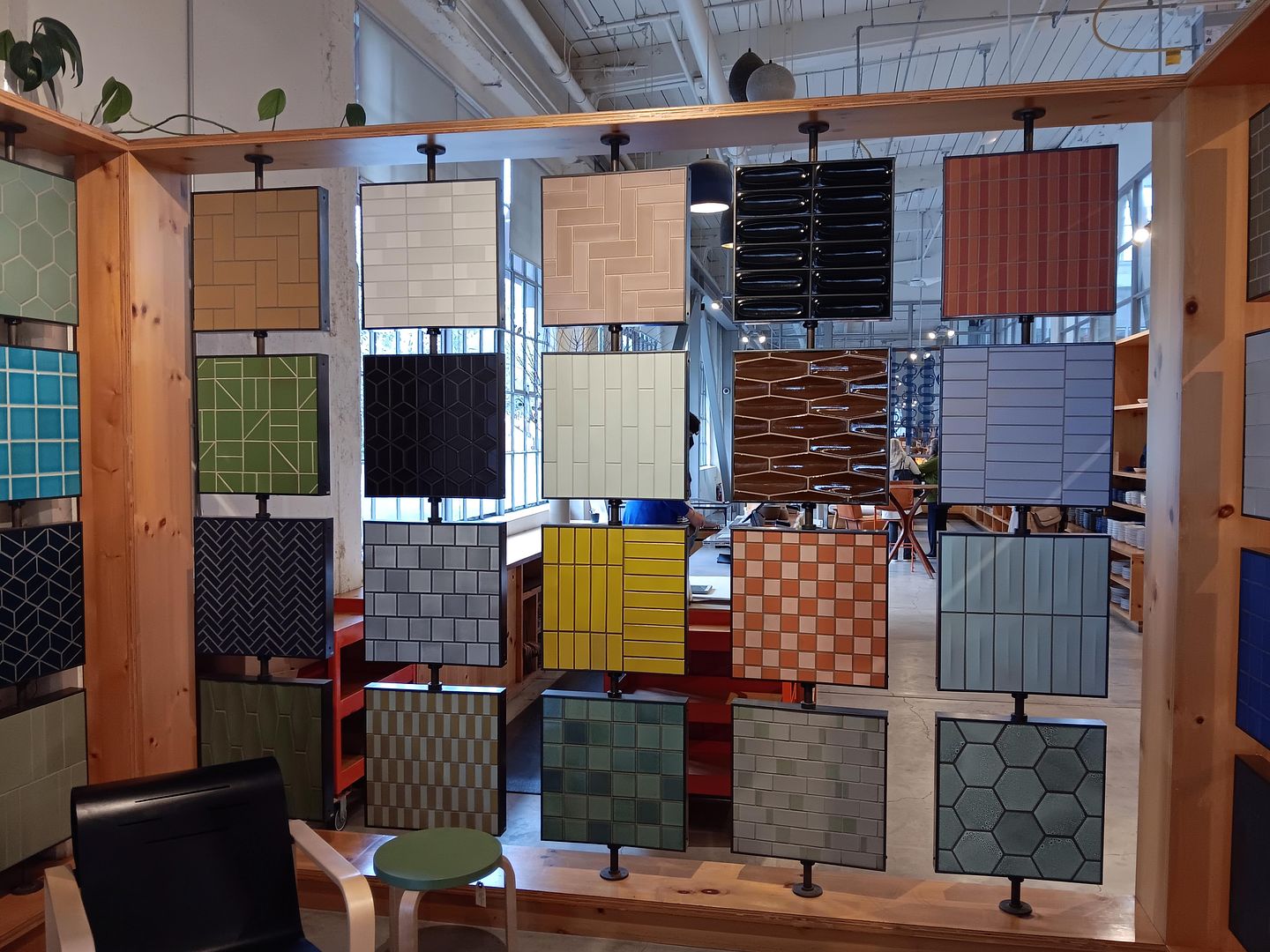
In addition to the fortune cookie factory tour in Chinatown, my friend and I decided to tour the Heath Ceramics factory in San Francisco's Mission District.
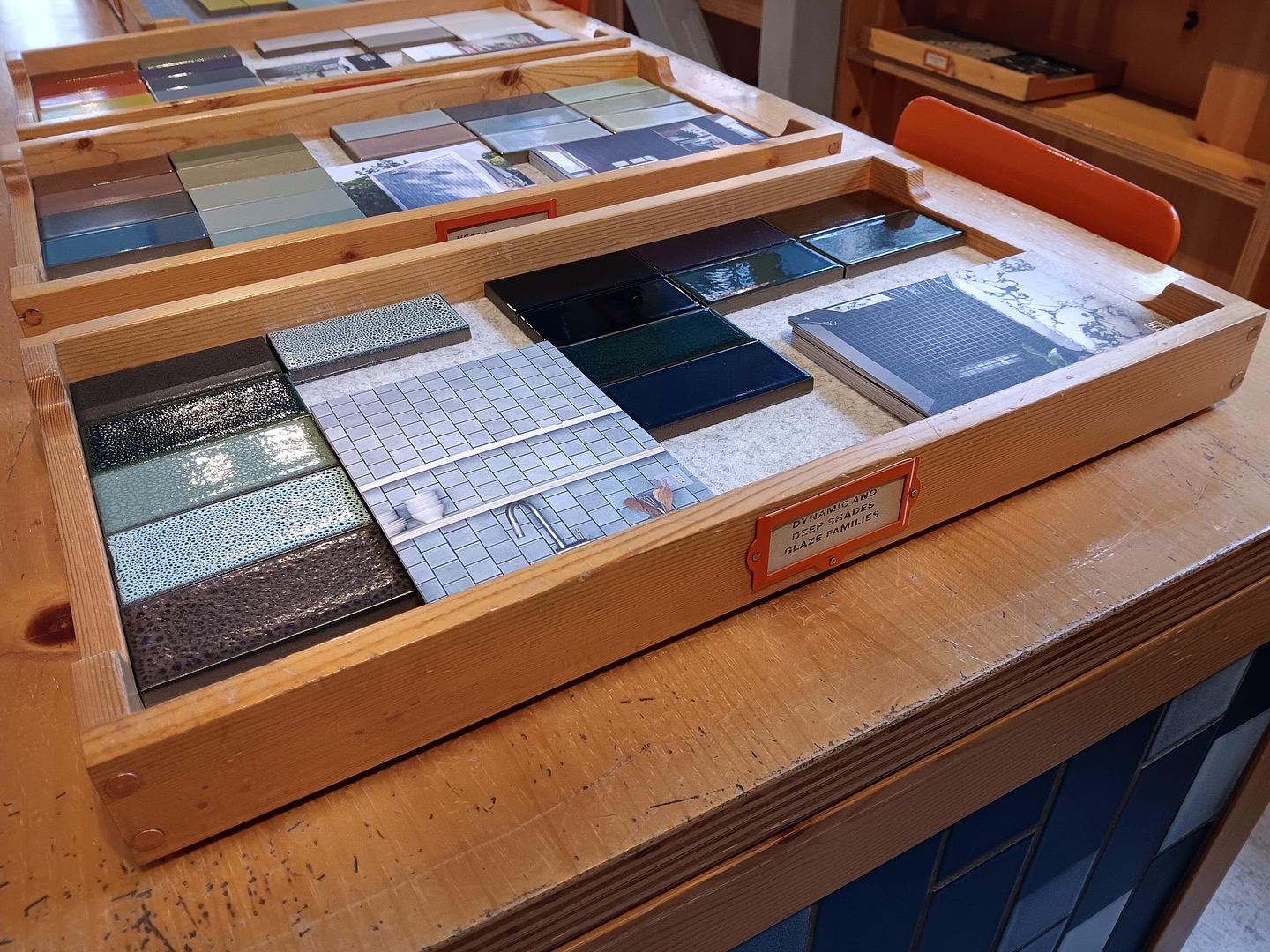
It's a newer facility for Heath, the ceramics studio that Edith Heath founded in 1945. She began on Clay Street in SF's Financial District—but in 1960 moved to a factory in Sausalito, where her dinnerware and pottery designs are still created today.
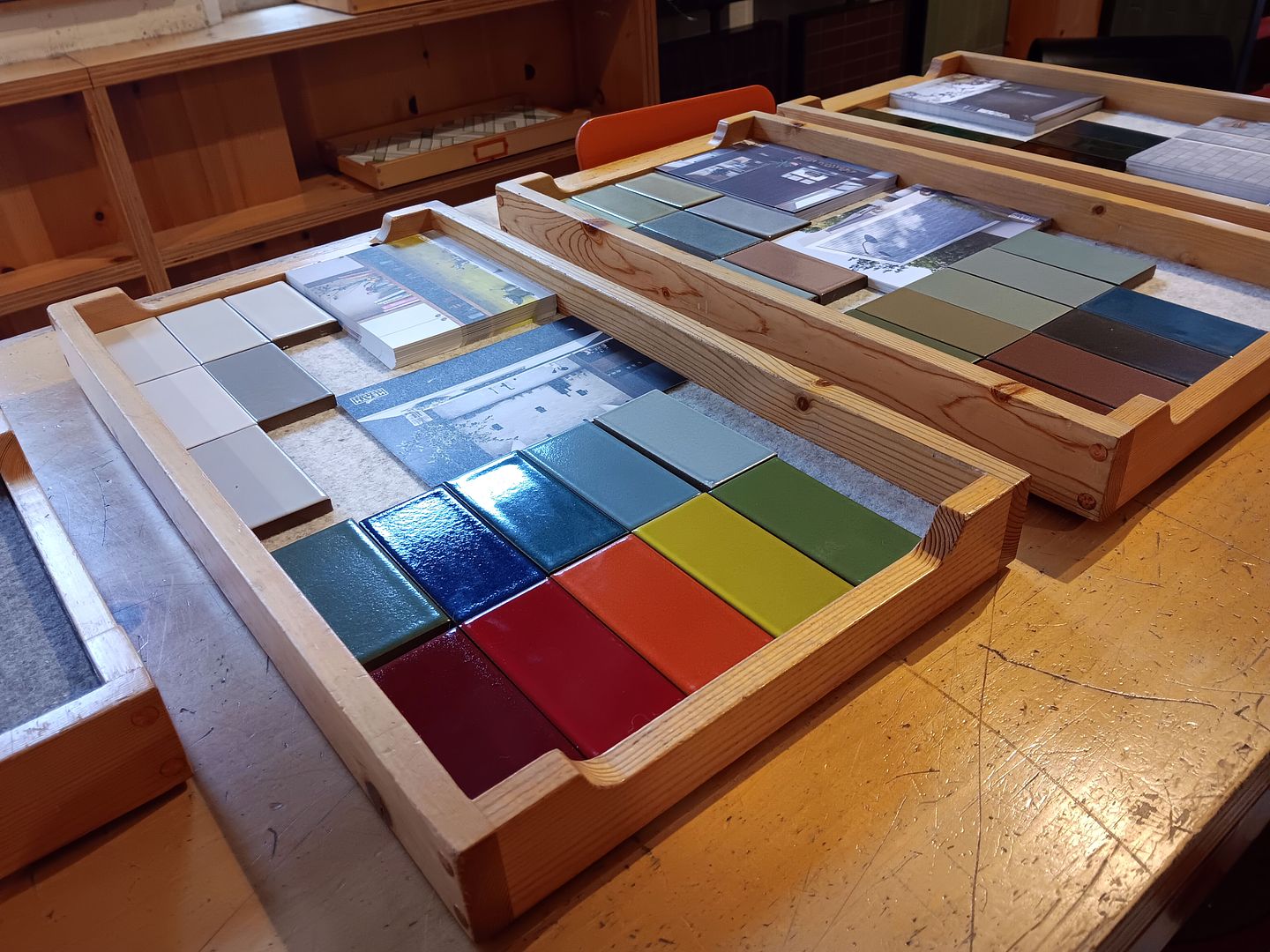
In 2003, Catherine Bailey and Robin Petravic bought and took over the Heath Ceramics business. Brian Heath had died in 2001, and Edith passed away in 2005 at age 94.
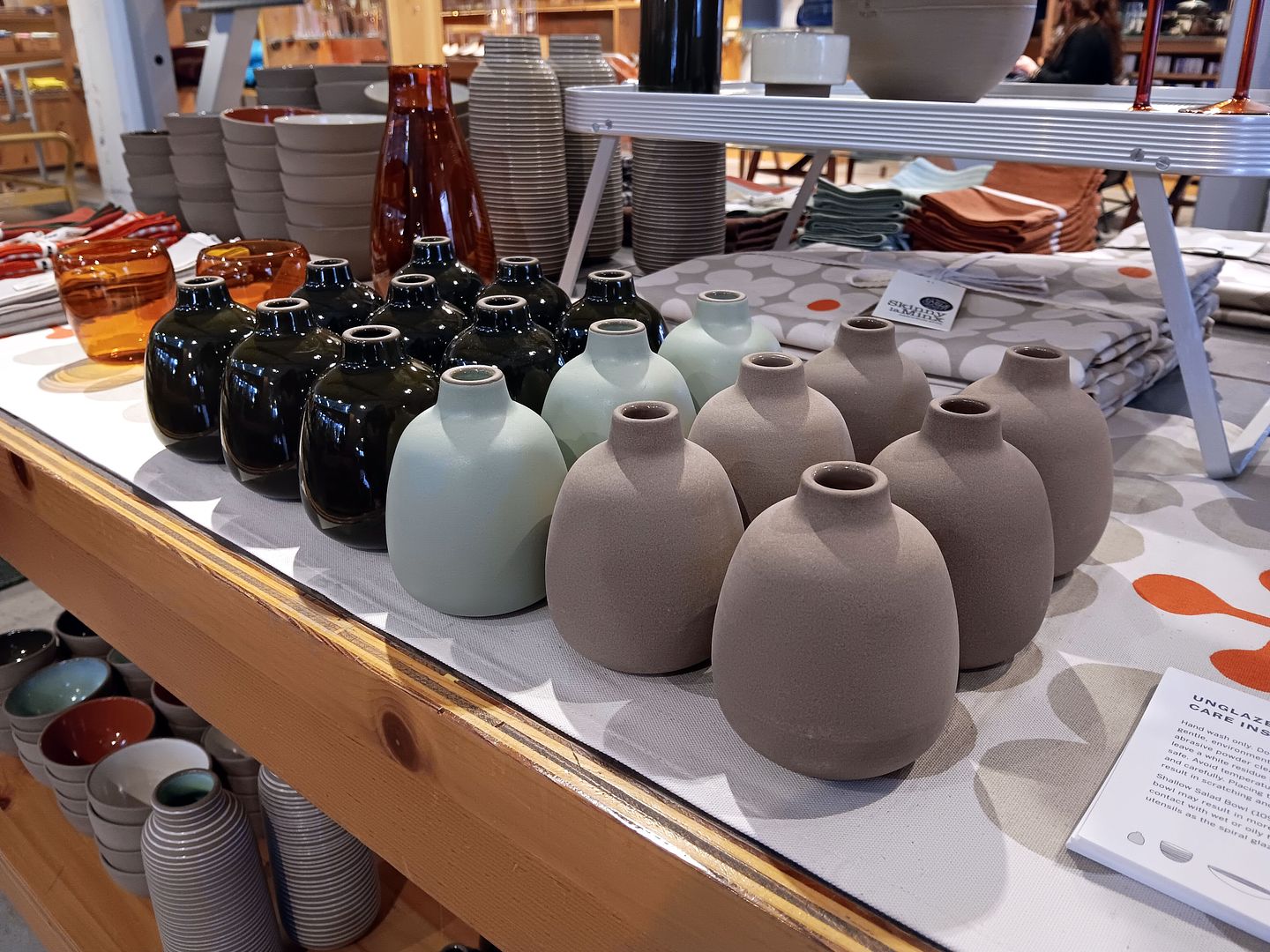
The Mission District facility on 18th Street, which opened in 2012, includes a factory that focuses on architectural stoneware tile, which Heath started manufacturing in 1967. Its adjacent showroom sells finished tiles, as well as cups, saucers, bud vases, and more.
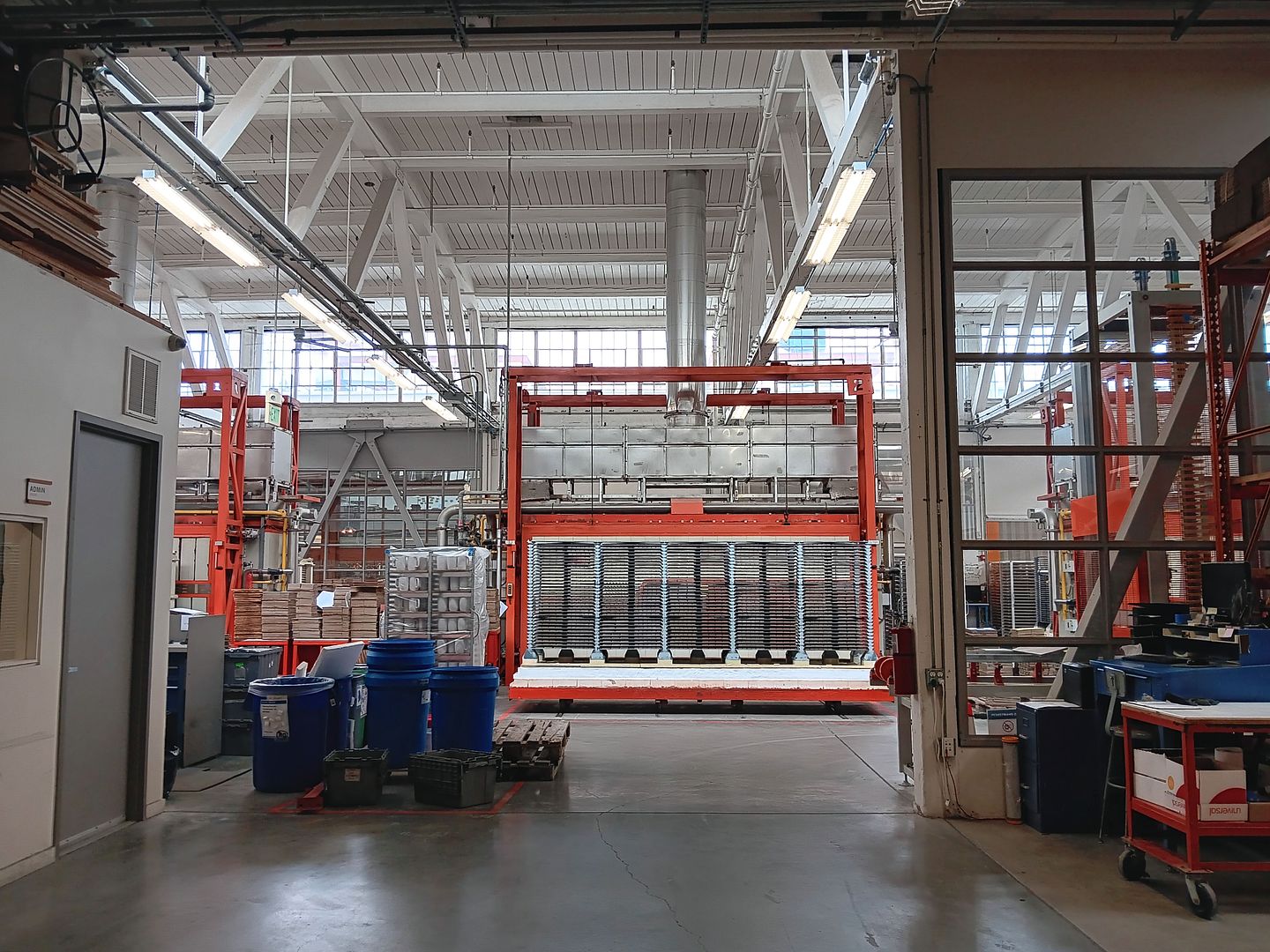
The 60,000-square-foot space used to house Mission Linen and Uniform Service...
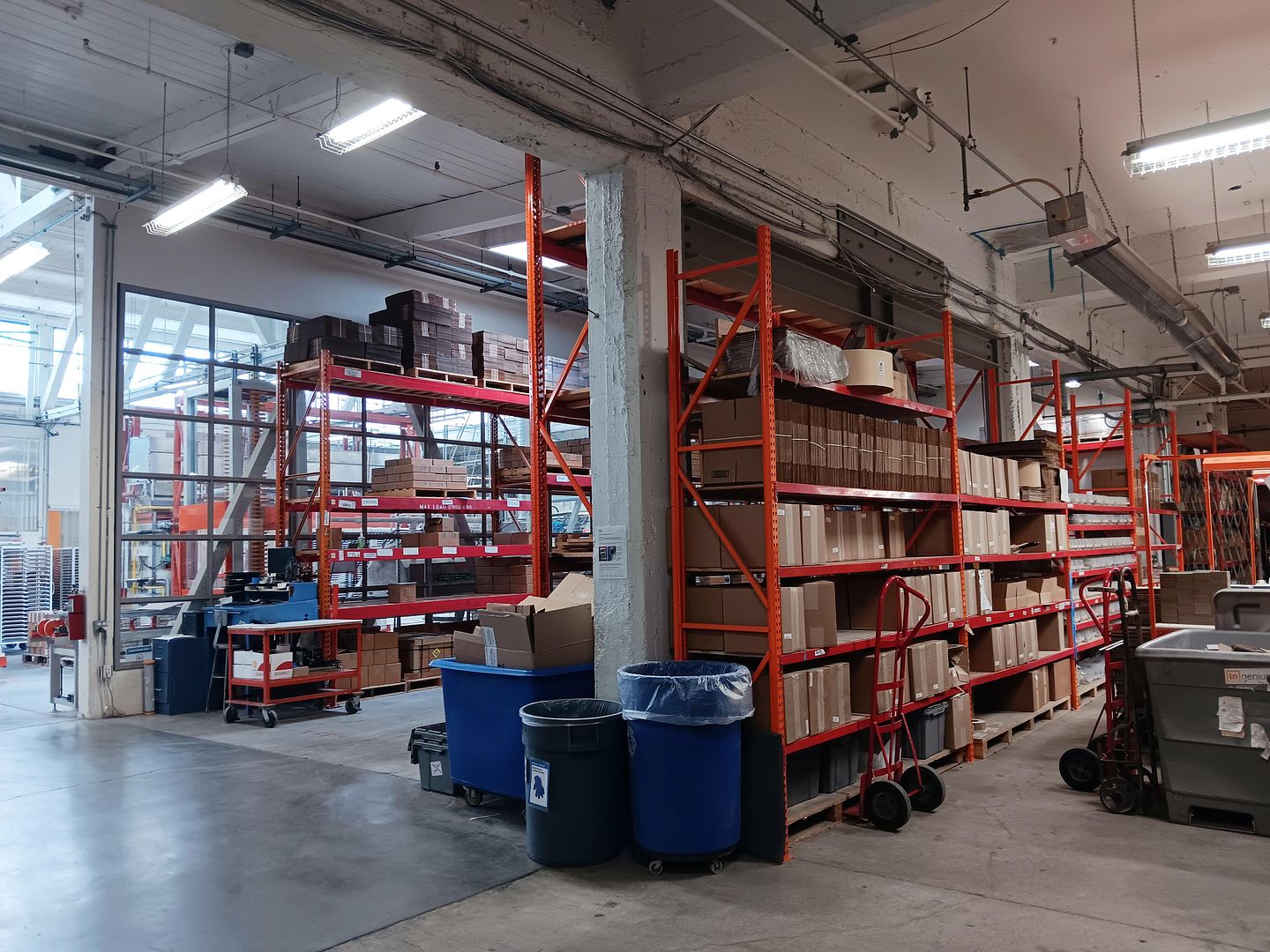
...a large-scale linen supply and laundry service operation.

Today, you can see where the floor's drainage trenches were filled in.
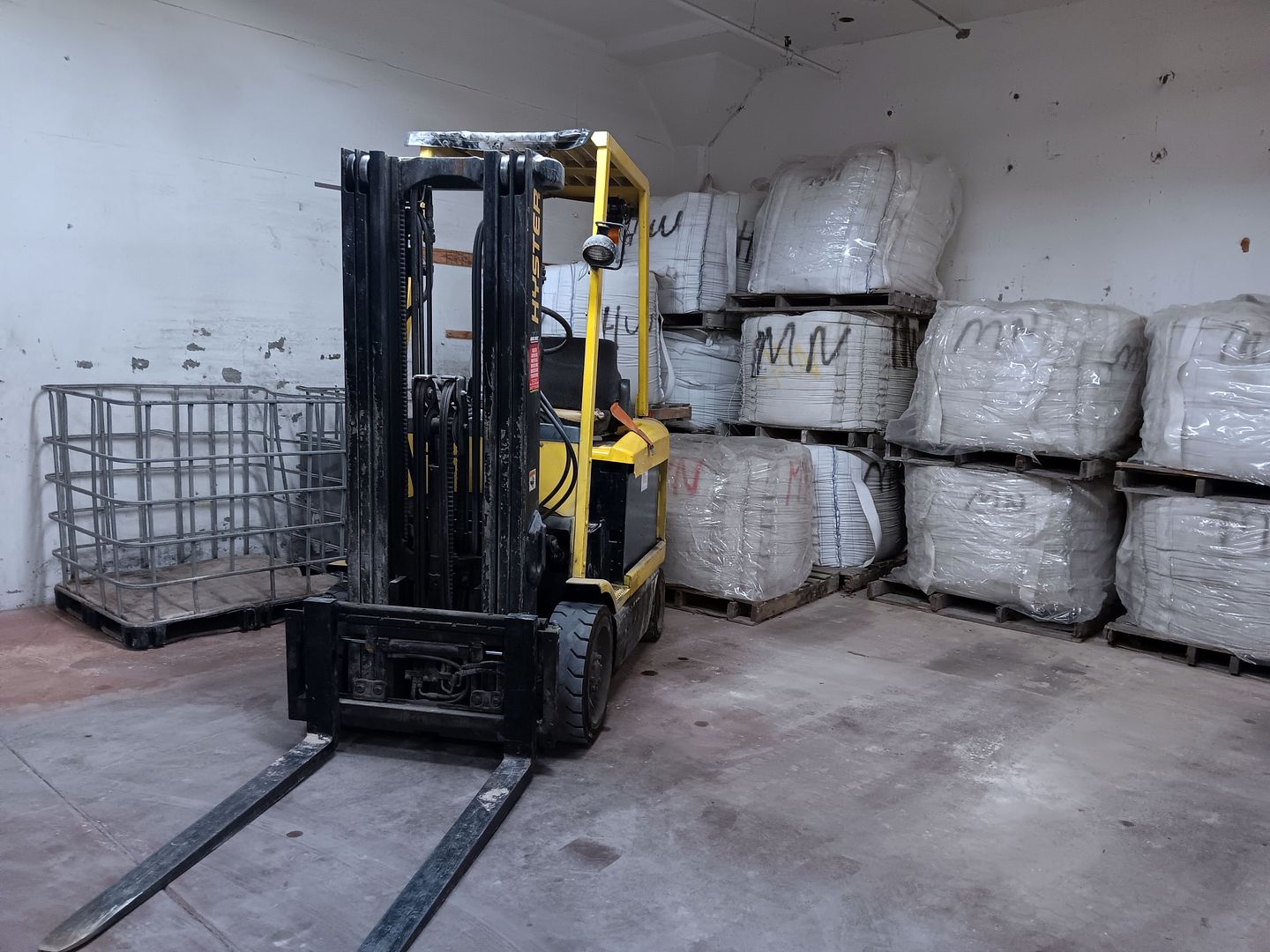
But instead of bales of lab coats, scrubs, and patient bedding, what's being forklifted now are blocks of clay powder, sourced from California clay pits.
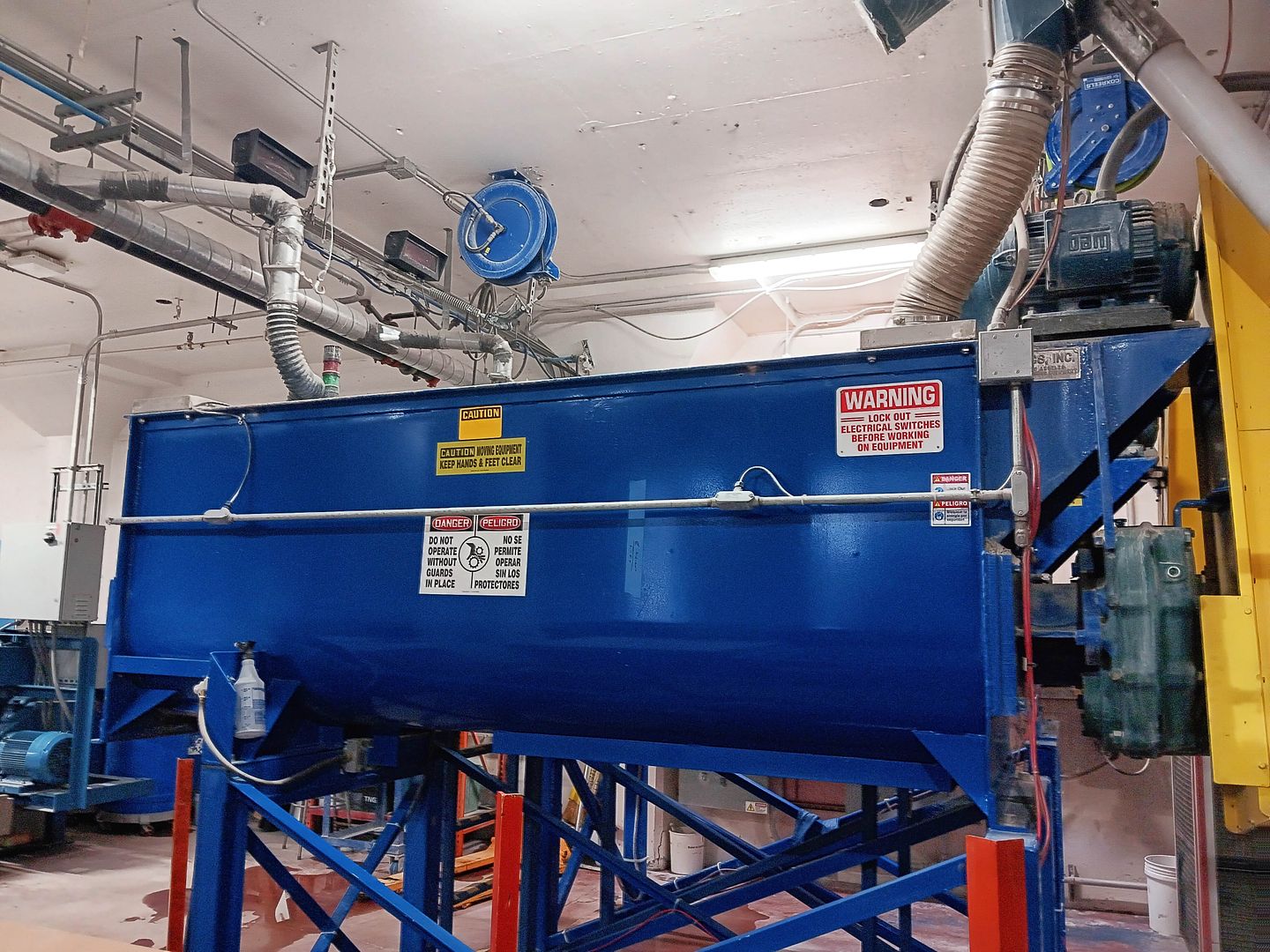
While most potters use a clay mixture created by someone else, Edith Heath was known for her own proprietary manganese clay body—a base ingredient that's still used today.
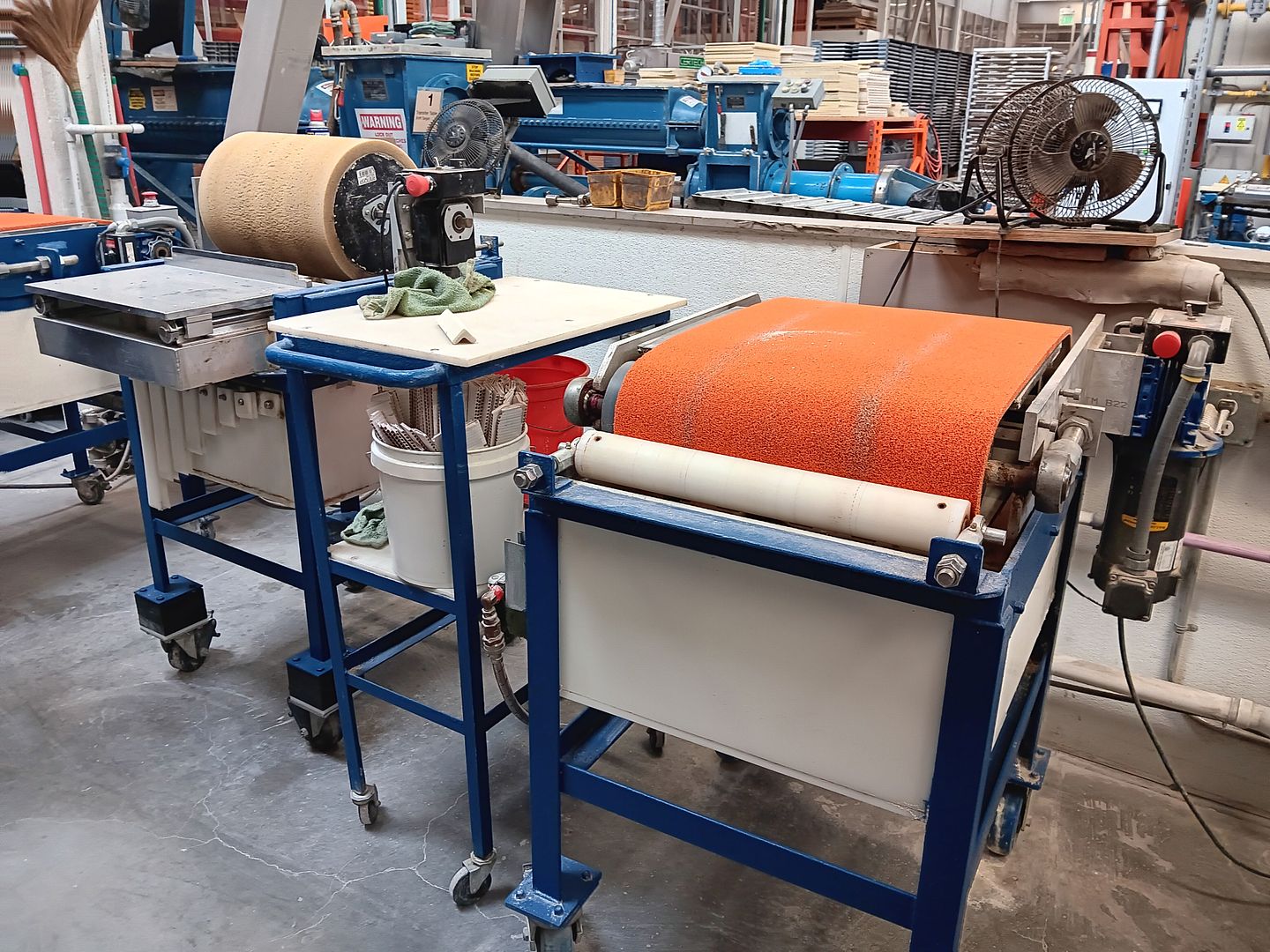
And although there are machines to help factory workers refine the thrown clay into the perfect shapes for tiles (especially those with rounded edges or any kind of beveling)...

...the process still very much relies on the human element, requiring the worker to stand for extended periods of time in front of a buffing sponge.
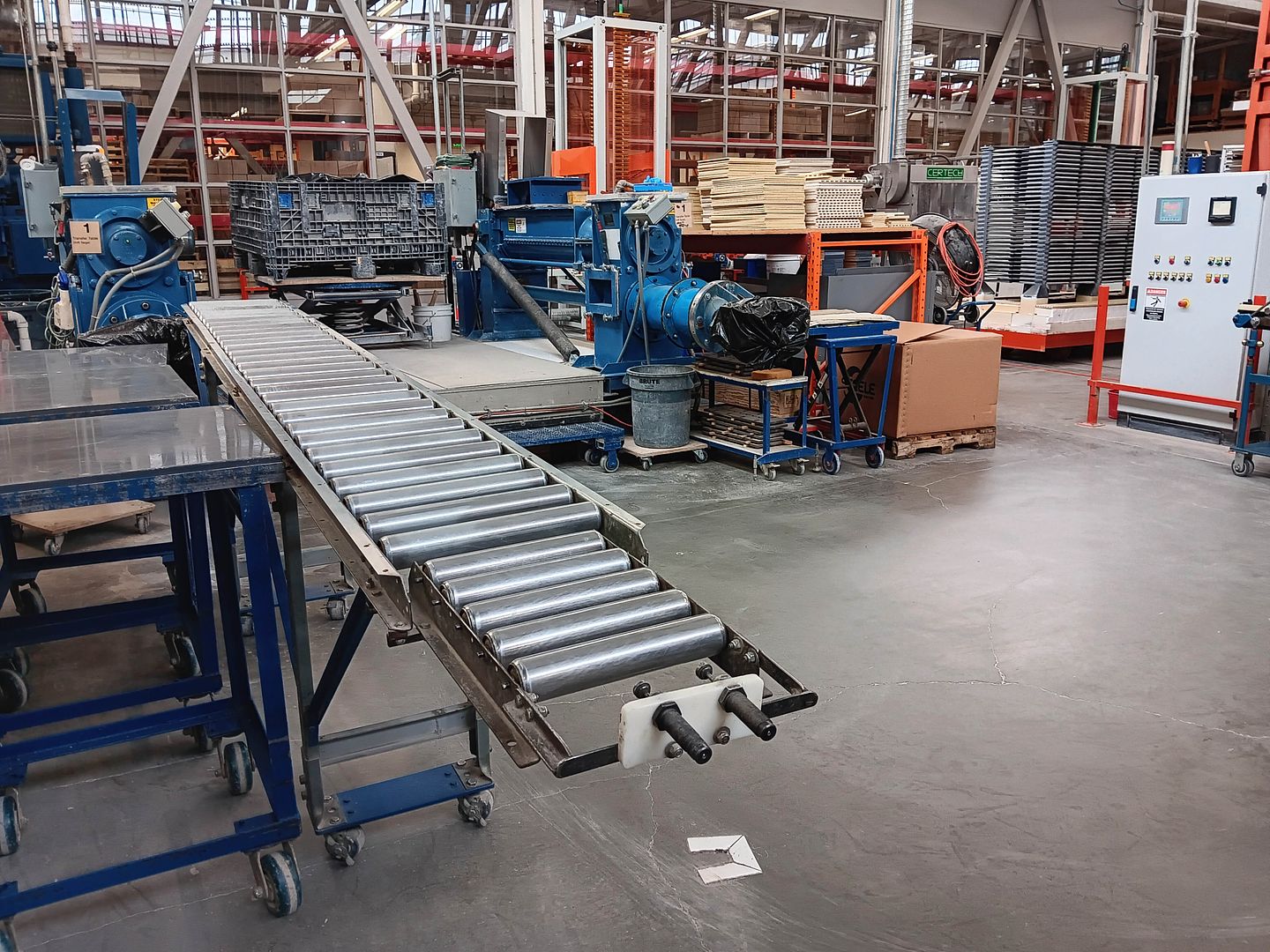
Even though the Heath philosophy is "blending human and machine," there's some equipment at the workers' disposal that they choose not to use.
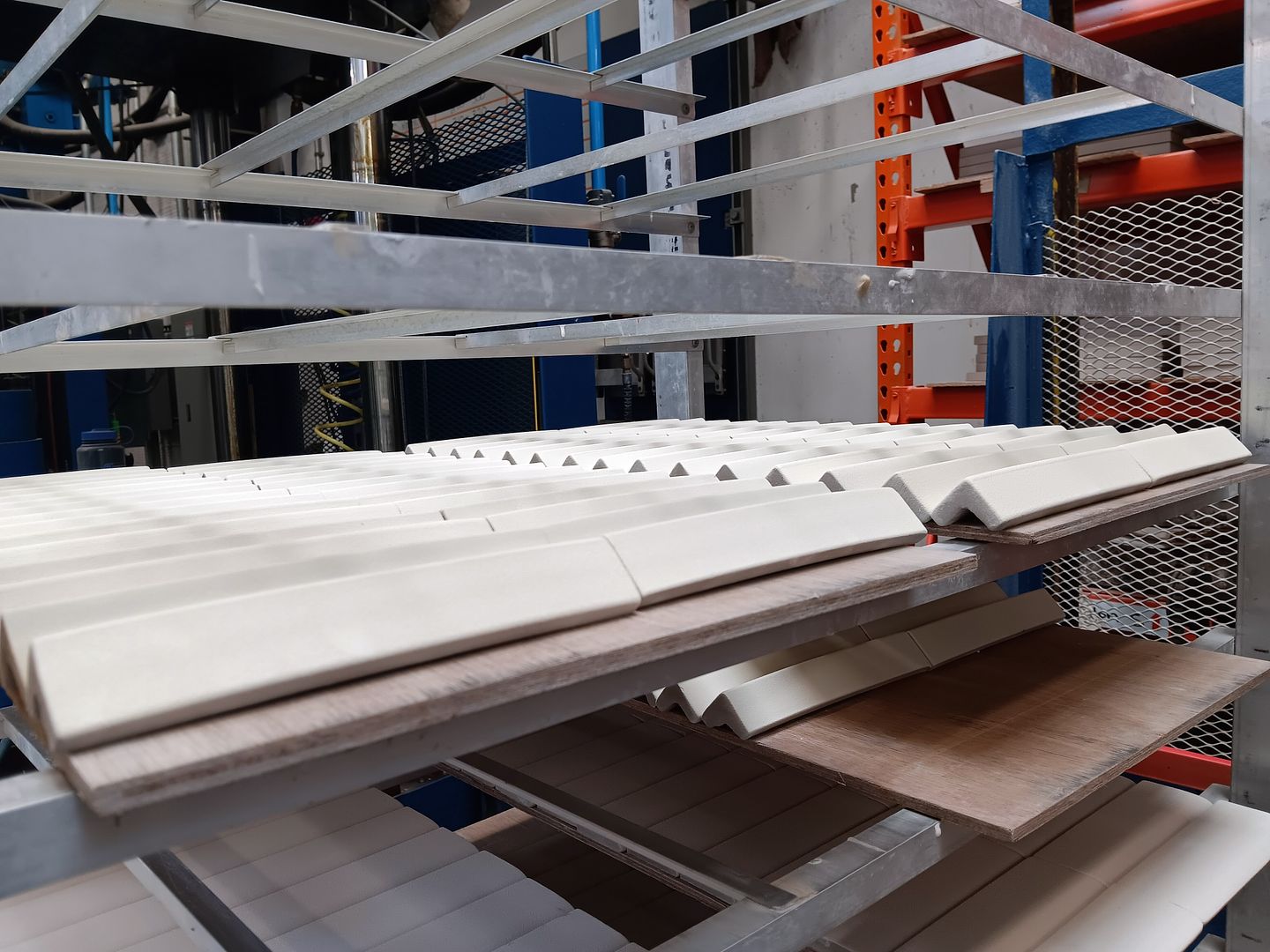
Since our visit was on a weekend day, the entire process was frozen in time...
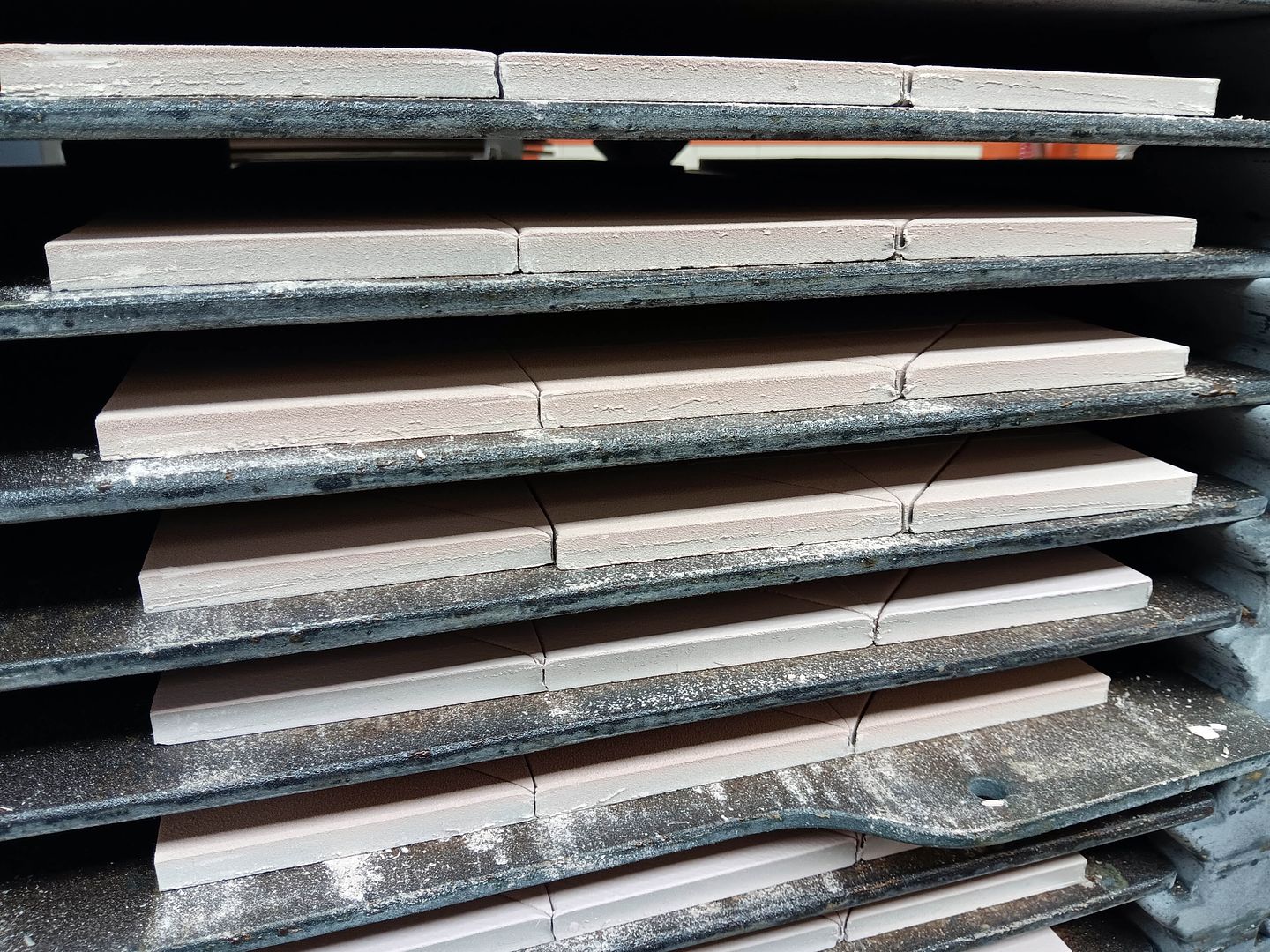
...with ceramic tiles and architectural edges, still works in progress, sitting on shelves like cookies cooling on bakers' racks.
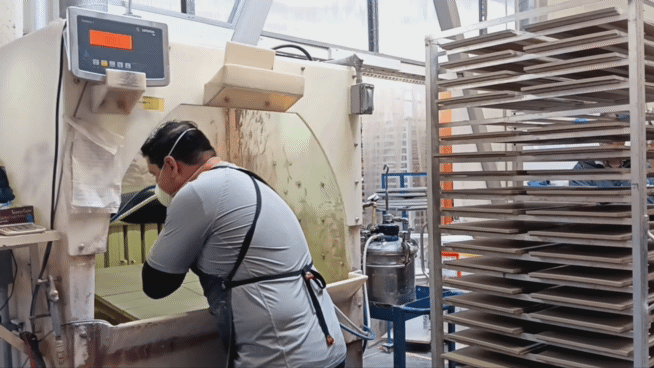
We were lucky enough to see some tiles getting spray-glazed by hand during our visit. This is an example of what Edith Heath and her husband Brian envisioned as "human-scale production."
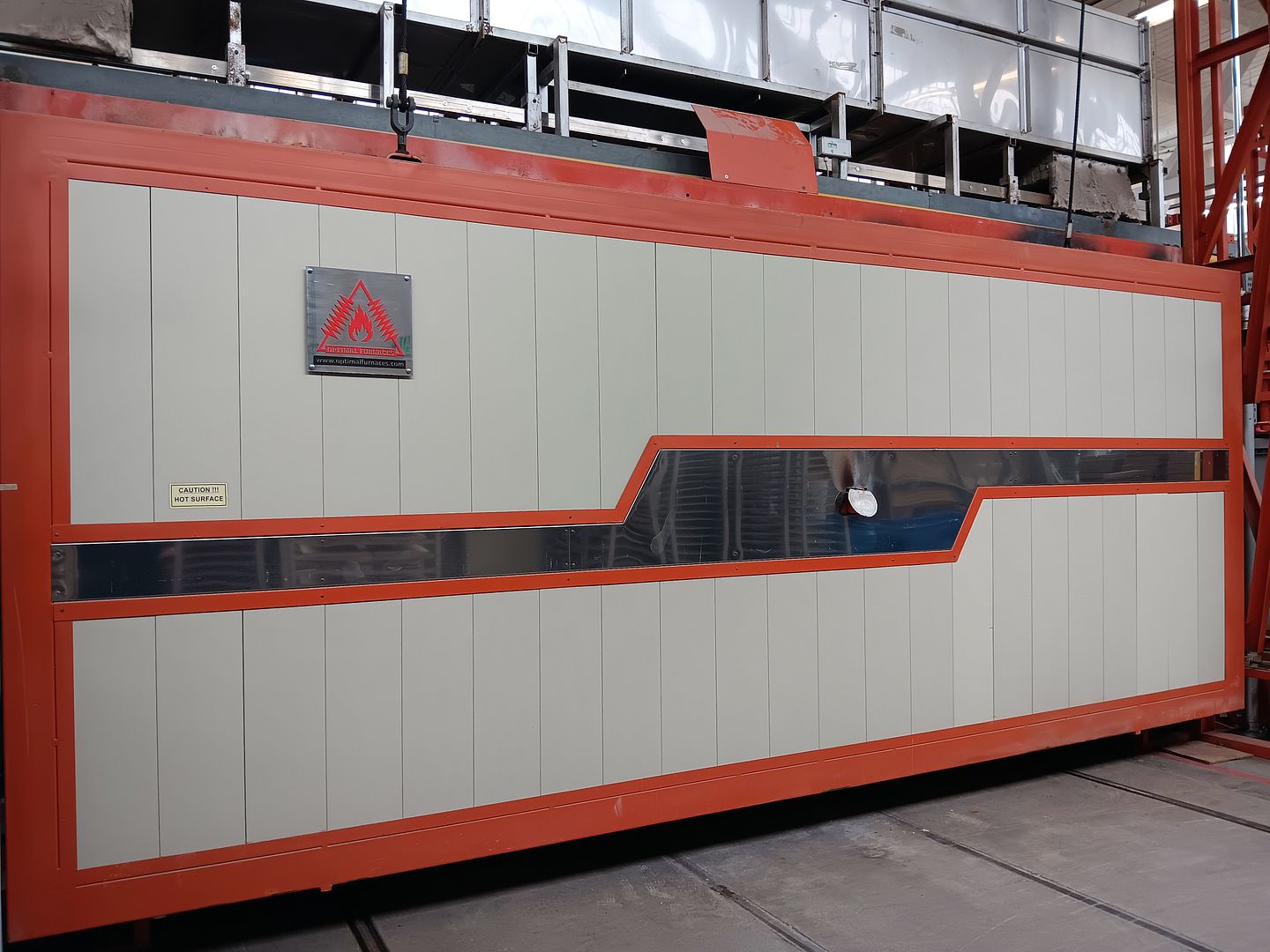
Fortunately, the kilns weren't running—otherwise those gigantic things would've been pumping out a lot of heat (even though they run at a lower temperature than standard, because of the proprietary clay).

Once the tiles are fired, they come out in a wide variety of finishes—and with some variation (within the bounds of Heath's standards), making each finished product unique (and "perfectly imperfect").
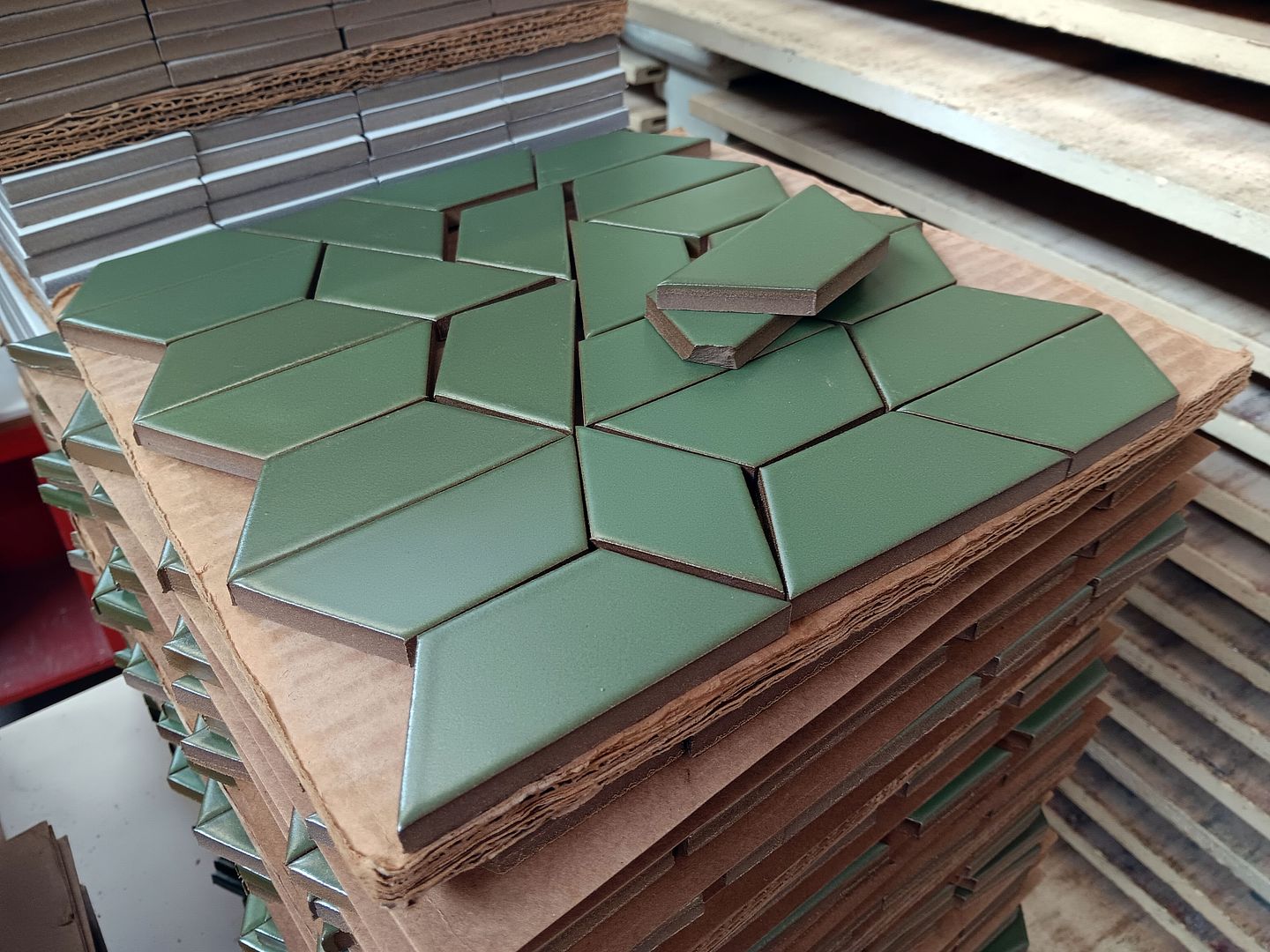
In addition to matte, semi-matte, and glossy finishes, there are also a variety of shapes (like "Little Diamond" and "Half Hex")...
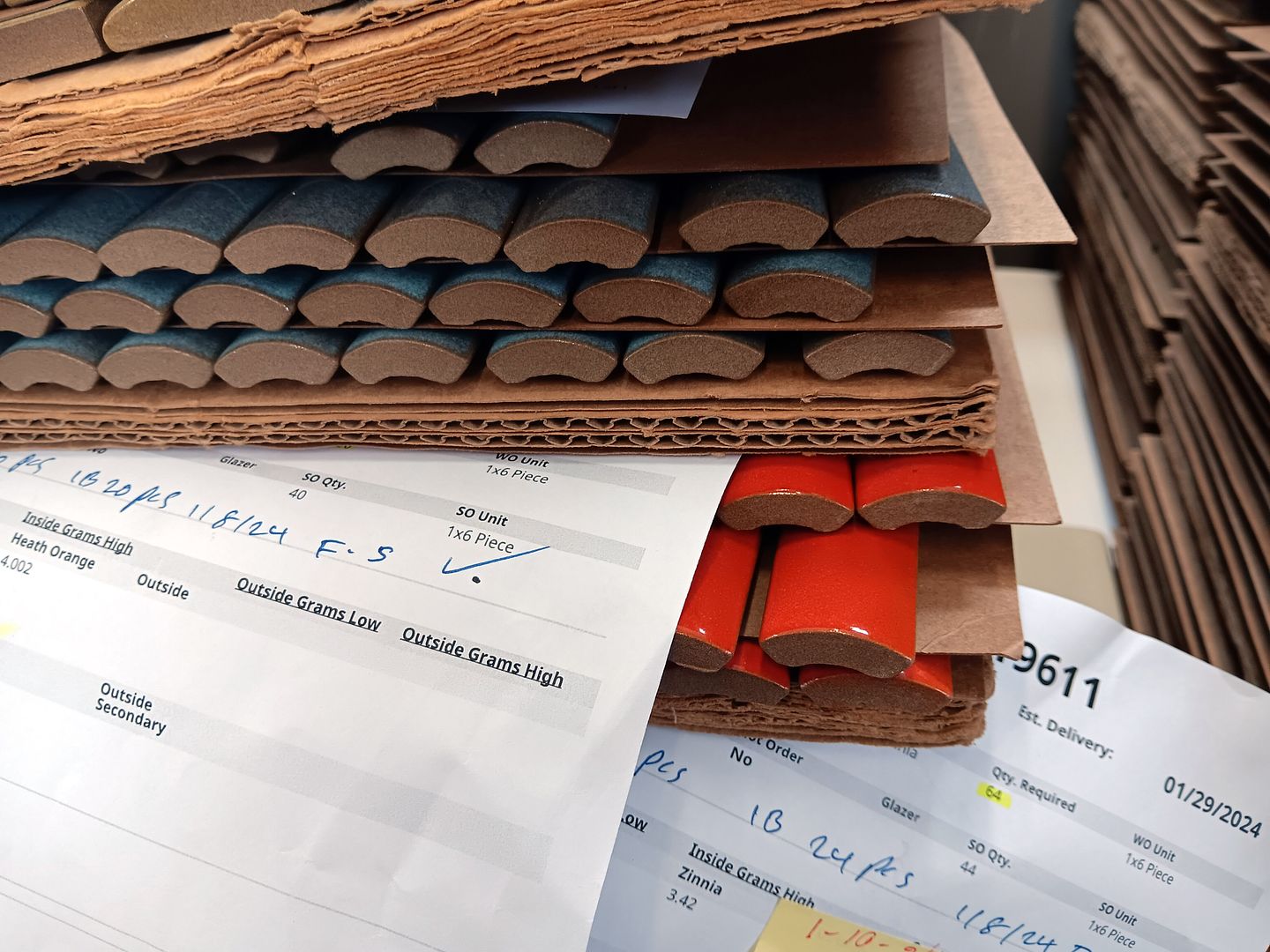
...trims (like bullnose edges, corner cove posts, and finger coves, above)...
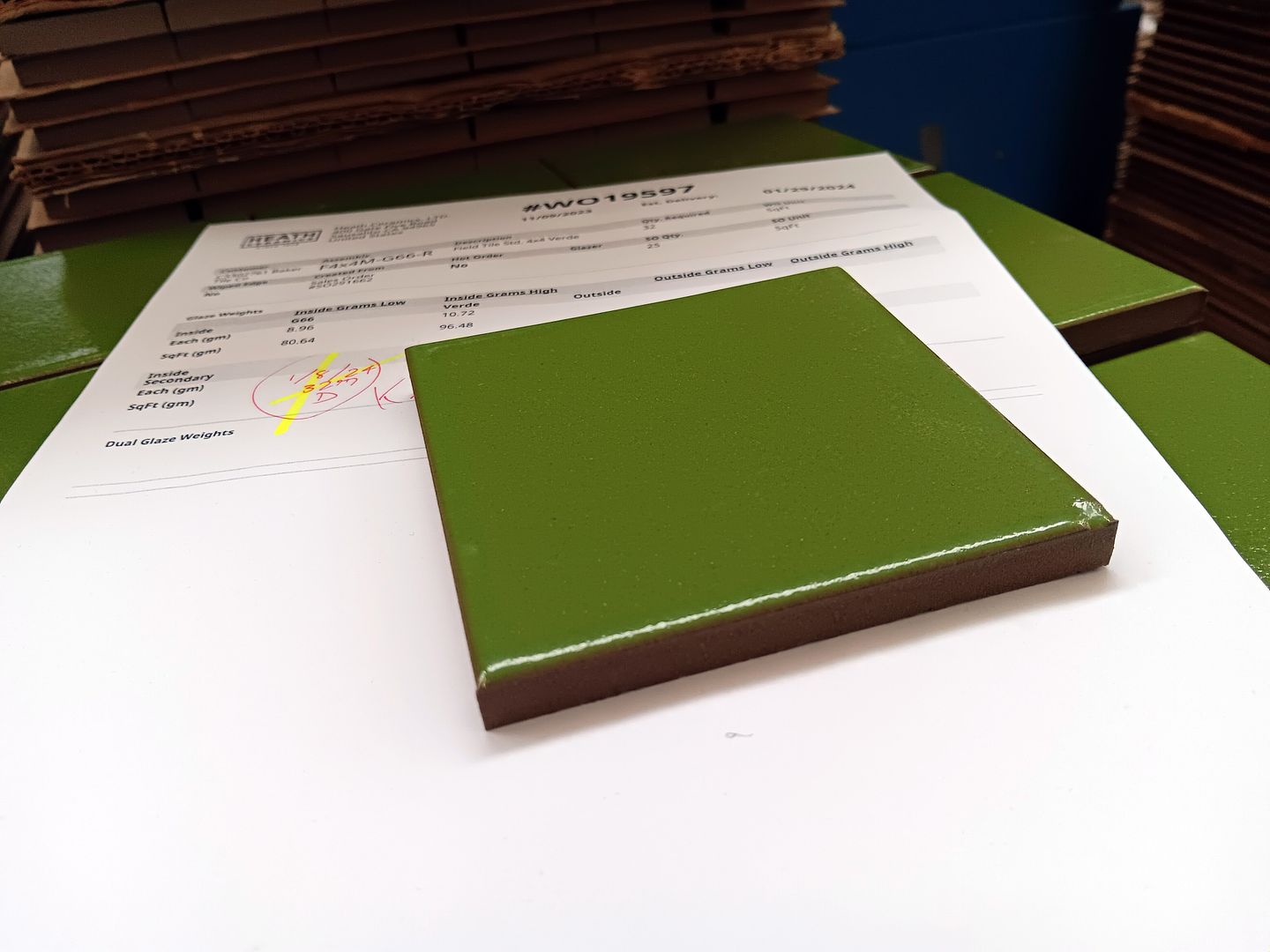
...and colors, from "Mid-Century White" to "Heath Orange" and "Zinna" to "Verde" (green), "Gloss Black," and beyond (including two-tone dual glazes), although the clay base is always brown.
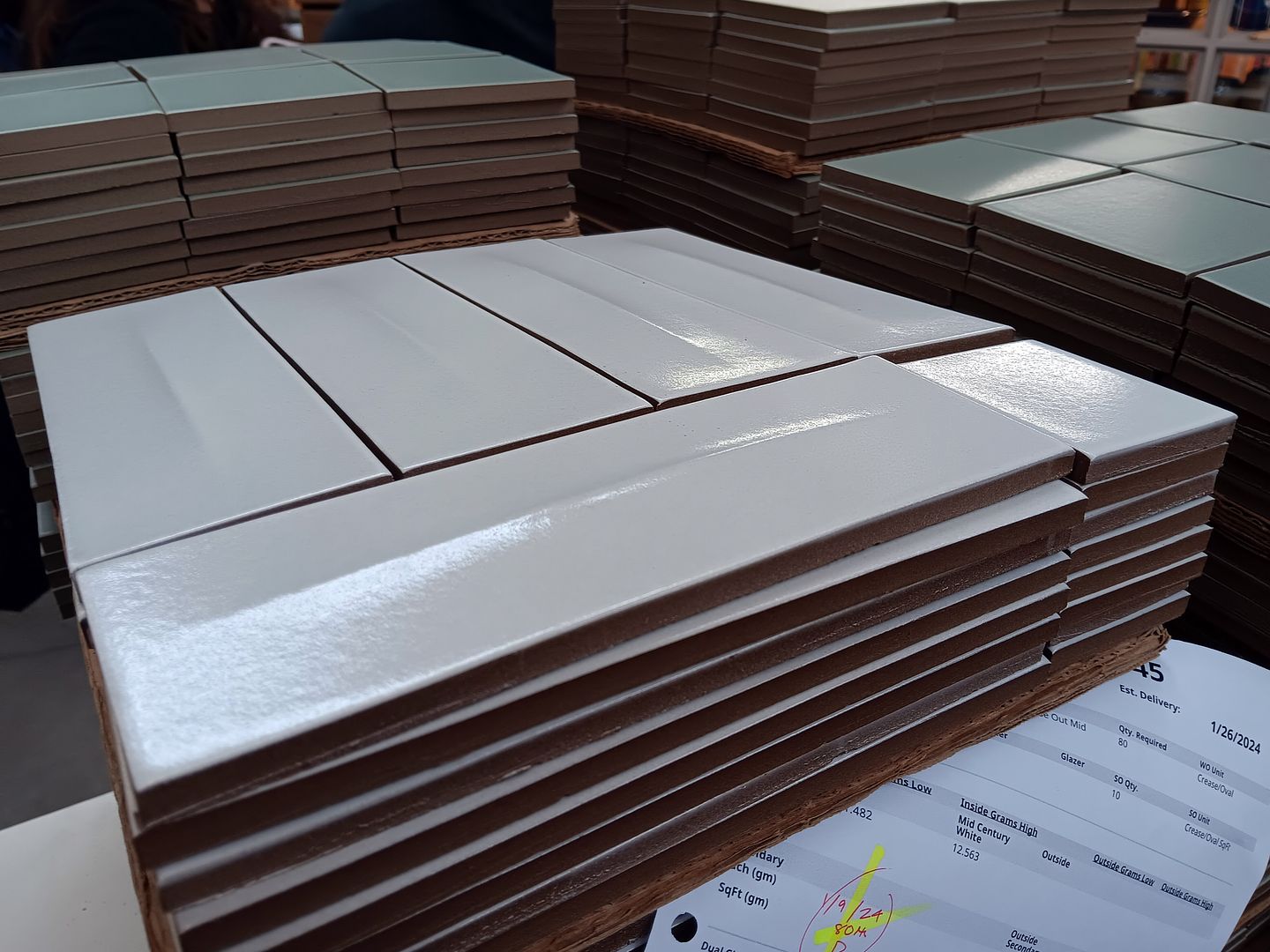
Dimensional tiles include those with a "crease out" (although you can also get ones with a "crease in").
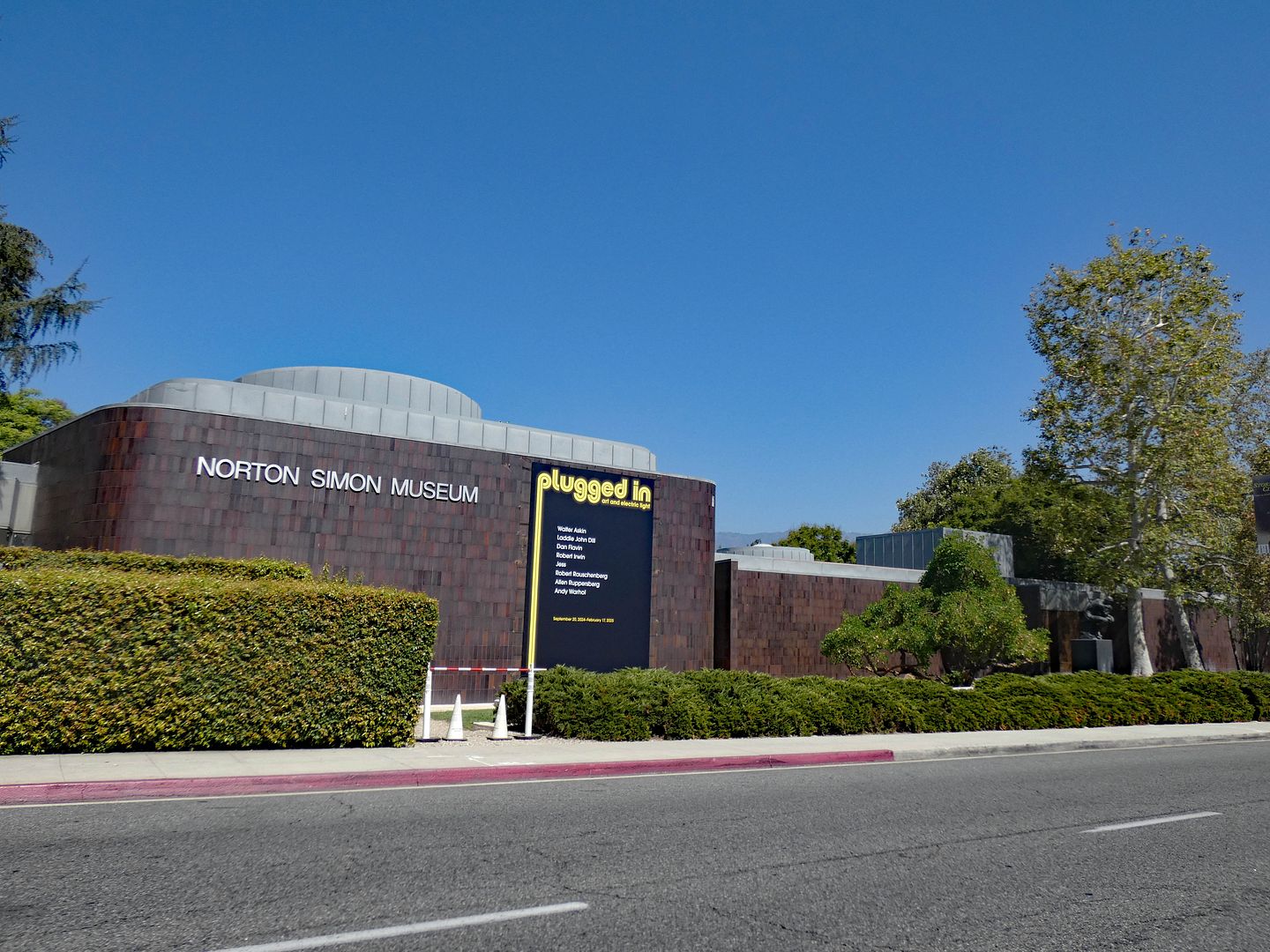
Want to see Edith Heath's work out in the real world?
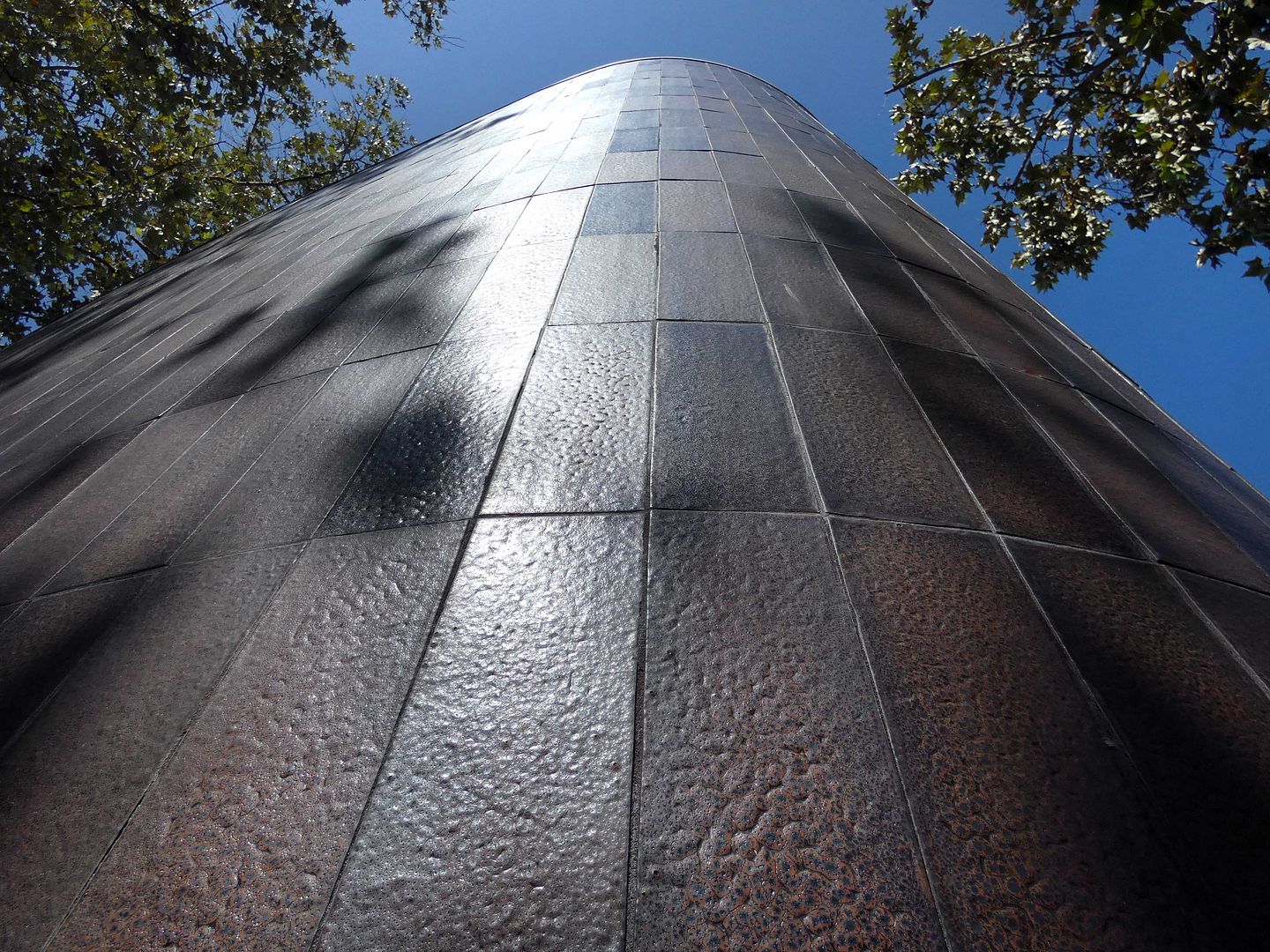
Check out her custom tile cladding on the outside of the Norton Simon Museum in Pasadena, California...
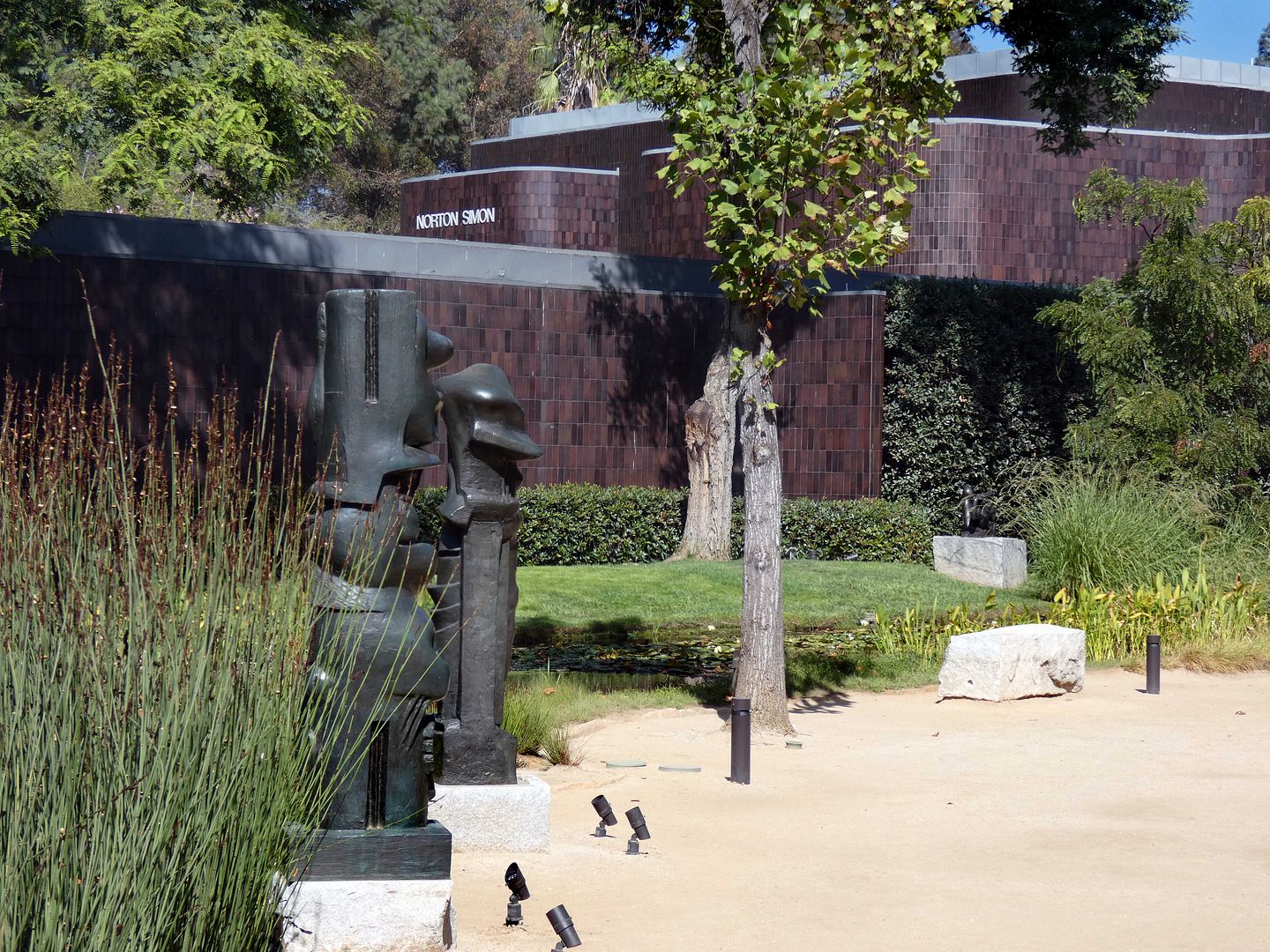
...which was formerly the Pasadena Art Museum, completed in 1969.
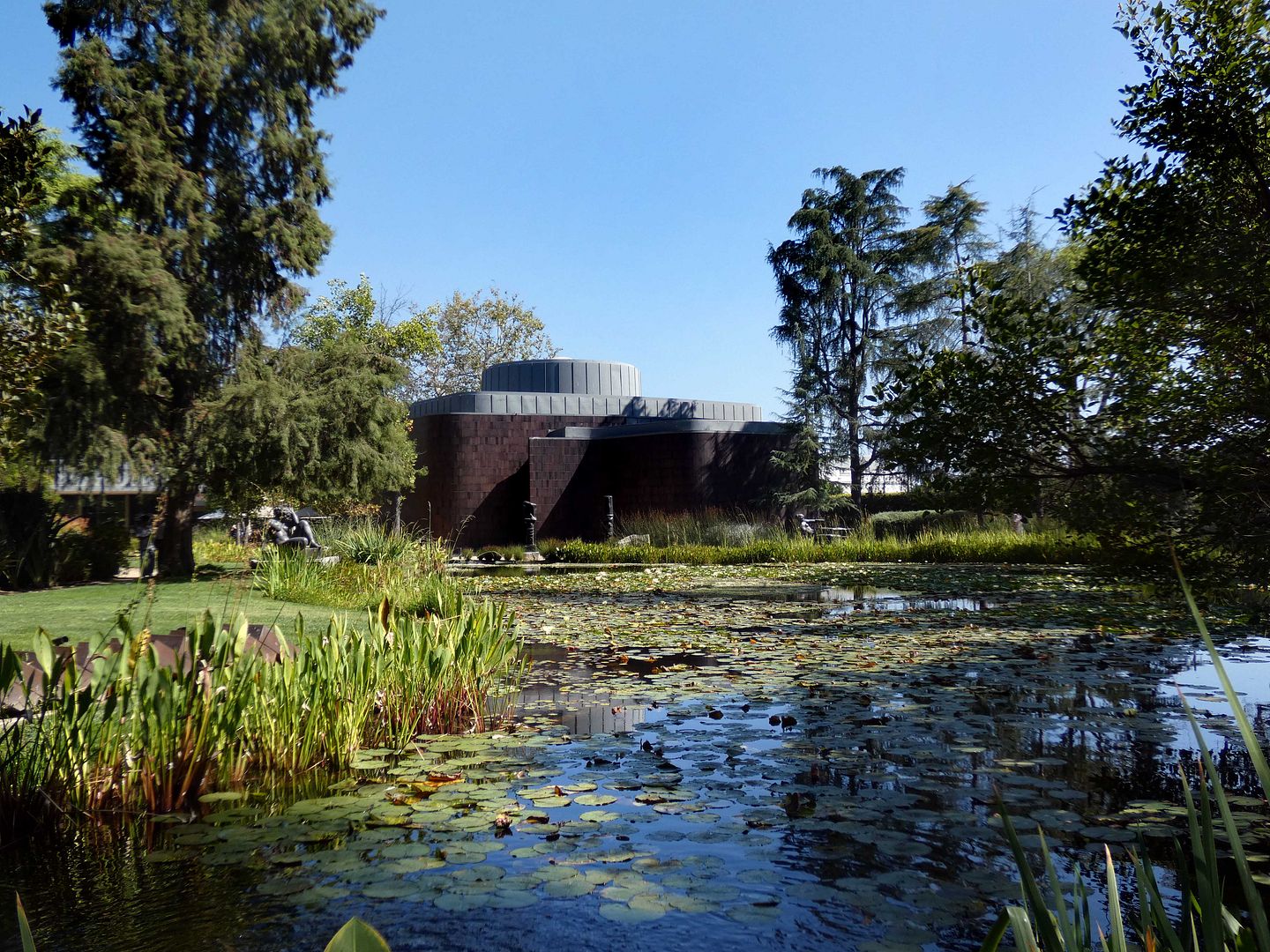
Its "stone" look is the result of Heath using layered glazes (Corten over Onyx).
Heath Ceramics was originally created to make tableware and pottery more accessible to the American public than, say, pricey porcelain or bone china. But now, vintage Heathware is incredibly valuable and can command top dollar.
And these days, new Heath wares aren't exactly affordable to everybody. But it's strong and durable—and made to last, no matter the temperature or weather. And even though it's coming out of a new leadership, it's still part of a historic legacy.
Related Posts:
No comments:
Post a Comment